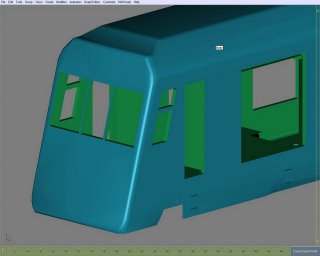
It was almost impossible to make the curved edge (all the way around) while keeping the front surface flat. A vertex even being out by only half a millimeter caused the uneven surface to reflect light in strange ways.
Due to the windows being cut out already, there are a lot of verticies on that front panel, and every time I chamfered the edges, they would move. I wish I had saved a screenshot of the bent front end so you could compare.
Finally I detached the front end from the rest of the model and cut it in half to reduce the area that I had to deal with. I set up a mirrored instance to complete the other half, so that any changes that I made one side, automatically happened on the other side too, and then I went around, vertex by vertex lining things up. I chamfered the edges one at a time (Each chamfer makes a new edge, there were four edges by the time I was done) and adjusted the verticies again after each chamfer. Finally I re-attached the front to the body, and welded everything together. A couple of tweaks later, and it looked like the picture.
I just hope it all holds together when I cut out the remaining holes (the one around the coupler is the big one).
So basically this week, a lot of time spent, but not a lot of progress. Still, its movement, and any forward movement is a good thing. You may notice a theme between this and the previous post. I guess the lesson to be learned is to cut out the holes LAST!! :)
The poly count is creeping up. My original estimate was around 8000. Im actively reducing polys as I go, and will try to keep it as low as possible. I also have to remember to move the cursor out of the way when I take the screen shots, to avoid getting tool-tips in the picture. Doh!
File Version: 276
Poly Count: 9200 (Excl bogies)
Thanks for the comments on the previous post. Its nice to know my work is on-target and is also being appreciated.

No comments:
Post a Comment